In November 2022, Nabla remotely resolved a production issue for its Malaysian customer, saving costs and time for the customer and improving their satisfaction.
The customer has long-term relationship with Nabla and places regular orders for packaging material from Nabla. During the use of a batch of Nabla's blank-fed packaging materials, scratches on the packaging materials were found during running on a filling machine, giving rise to customer’s concern about packaging material quality.
Swiftly stepping into action, Nabla Technical team tackled this issue within an hour. The engineer conducted initial investigations liaising with Nabla Quality Assurance team and factory to inspect the samples of this batch of packaging material. Nabla Quality Assurance team ed that the packaging material was of standard quality, ruling out possibility of inherent packaging material defects.
Nabla Technical team then initiated a remote video inspection with the customer for further examination. Upon observing the scratches on the packaging material and the customer’s filling machine, the technical experts determined that the scratches were caused by a specific component of the filling machine. Under the technical team's guidance, the customer's production staff dismantled the suspected part, polished it, and reinstalled it, effectively resolving the issue of scratches.
Traditional technical service might require dispatching engineers to the site, incurring costs such as travel and accommodation cost of engineers, purchase of new spare parts, and losses from production downtime, which could easily accumulate to thousands of dollars. In contrast, Nabla's remote technical service was rapid, economical, and effective.
Nabla has a three-tiered approach to problem resolution. For minor issues, remote video inspections offer a swift and efficient solution. If the remote inspection is not enough to fix the issue, Nabla deploys locally-based engineers to conduct onsite checks. If the issue still exists, Nabla will dispatch distinguished technical experts from its global team, who possess over 15 years of experience and with proficiencies covering both mechanical and electronic engineering.
Every second equates to costs in the fast-paced world of liquid food industry. From problem presentation to solution, the entire process was completed within 12 hours. The Malaysian customer was delighted with the , cost-saving and efficient service, leading to increased trust and further procurement of packaging materials and spare parts from Nabla. Nabla has continued to prove itself as a trusted partner in the global liquid food packaging industry with its professional technician resources sharing and coverage.
The customer has long-term relationship with Nabla and places regular orders for packaging material from Nabla. During the use of a batch of Nabla's blank-fed packaging materials, scratches on the packaging materials were found during running on a filling machine, giving rise to customer’s concern about packaging material quality.
Swiftly stepping into action, Nabla Technical team tackled this issue within an hour. The engineer conducted initial investigations liaising with Nabla Quality Assurance team and factory to inspect the samples of this batch of packaging material. Nabla Quality Assurance team ed that the packaging material was of standard quality, ruling out possibility of inherent packaging material defects.
Nabla Technical team then initiated a remote video inspection with the customer for further examination. Upon observing the scratches on the packaging material and the customer’s filling machine, the technical experts determined that the scratches were caused by a specific component of the filling machine. Under the technical team's guidance, the customer's production staff dismantled the suspected part, polished it, and reinstalled it, effectively resolving the issue of scratches.
Traditional technical service might require dispatching engineers to the site, incurring costs such as travel and accommodation cost of engineers, purchase of new spare parts, and losses from production downtime, which could easily accumulate to thousands of dollars. In contrast, Nabla's remote technical service was rapid, economical, and effective.
Nabla has a three-tiered approach to problem resolution. For minor issues, remote video inspections offer a swift and efficient solution. If the remote inspection is not enough to fix the issue, Nabla deploys locally-based engineers to conduct onsite checks. If the issue still exists, Nabla will dispatch distinguished technical experts from its global team, who possess over 15 years of experience and with proficiencies covering both mechanical and electronic engineering.
Every second equates to costs in the fast-paced world of liquid food industry. From problem presentation to solution, the entire process was completed within 12 hours. The Malaysian customer was delighted with the , cost-saving and efficient service, leading to increased trust and further procurement of packaging materials and spare parts from Nabla. Nabla has continued to prove itself as a trusted partner in the global liquid food packaging industry with its professional technician resources sharing and coverage.
النقاط الرئيسية
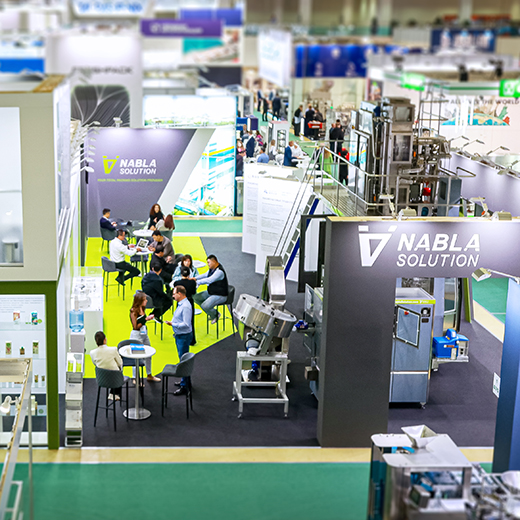
Nabla Solution introduces its total packing solution at Agroprodmash 2023
Nabla Solution has showcased its product portfolio to liquid food producers at Agroprodmash 2023, from 9-13 October.
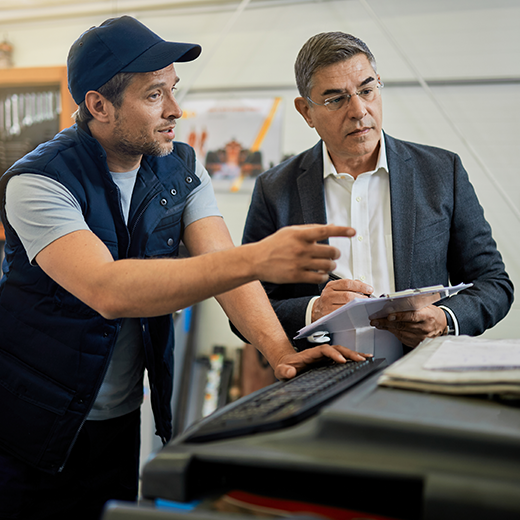
Technical service for Malaysian dairy producer
Local technical team inspected and solved the machine shutdown at the customer's site in fast response